The injection molding machine is one of the most popular and efficient manufacturing processes in the world and can produce large quantities of the products you are using every day. Injection machines are capable of producing identical volumes of items in the fastest time while maintaining product quality. Do you know how does injection moulding machine work? Let’s learn the principle of injection machine operation with BNT Machinery in this article.
Contents
- 1 What is an injection molding machine?
- 2 History of injection molding
- 3 Application of injection molding technology
- 4 How does injection moulding machine work?
- 5 Suitable plastics
- 6 Advantages and limitations of using an injection molding machine
- 7 Contact information to buy an injection molding machine:
What is an injection molding machine?
An injection molding machine is production equipment capable of producing large volumes of products. It works by injecting molten material into the mold. Injection molding materials include metals, glasses, and elastomers, and are most commonly used to create thermoplastics and thermosetting polymers.
> > > Learn more: How does CO injection machine affect tuna color?
History of injection molding
The injection molding machine was first invented in the United States in 1872 by brothers John Wesley Hyatt and Isaiah. This machine is more primitive than modern equipment, it works like a large needle, under the action of a piston, the plastic through the cylinder is heated and injected into the mold.
German scientists Arthur Eichengrün and Theodore Becker discovered the first soluble forms of cellulose acetate in 1903, which are less flammable than cellulose nitrate and easy to extrude. Arthur Eichengrün developed the first injection molding machine in 1939 and patented the flexible cellulose acetate injection mold.
World War II opened up huge demand for cheap and mass-produced products. In 1946, American inventor James Watson Hendry built the first screw pump, which allowed more precise control of the injection rate and quality of the products manufactured. This machine can also mix raw materials before spraying, so that colored plastic or recycled plastics are mixed.
In 1970, Hendry developed the first air-assisted injection molding system for rapid cooling of complex products. This improves the design flexibility and rigidity of manufactured products while saving on costs, fuel, raw materials, and waste.
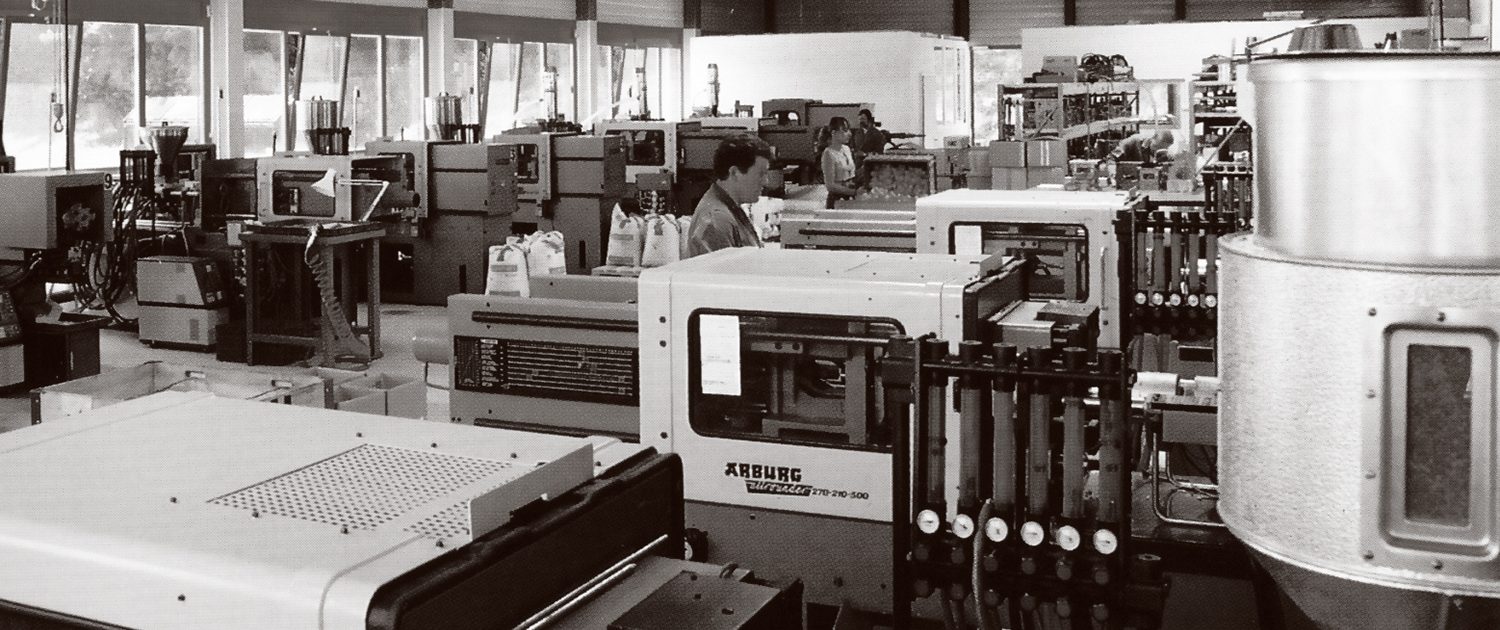
History of plastics injection molding
In 1990, aluminum molds were widely used. Nowadays, screw pumps make up the majority of plastic injection molding machines.
Plastic injection molding technology produces push buttons for use in automotive, medical, aerospace, consumer goods, toys, plumbing, packaging, and construction.
Application of injection molding technology
Injection molding technology is widely used in industry, especially in the plastics industry, as the ideal method for producing large objects of the same volume. In addition, injection molding technology is also applied in the manufacturing industry of packaging, bottle caps, auto parts, components, coils, musical instruments, tables and chairs, machine parts (including gears), …
> > > Read more: What is an overmold? What are the applications of overmolding?
How does injection moulding machine work?
How does injection moulding machine work? The injection molding process is carried out through 4 main steps, specifically as follows:
Step 1: Use the plastic injection machine to melt the material to a suitable temperature.
In this step, the raw materials that are still in a hard form such as recycled plastics and virgin plastic will be put into the raw material port of the plastic injection machine. Here, the materials will be mixed and pushed forward to melt by the heating system arranged around the cylinder of the machine.
Step 2: The screw system of the plastic injection molding machine will create a large pressure to inject the molten plastic into the mold in the closed state. The screw system of the plastic injection machine will act as a plunger pushing the melted plastic forward with great pressure. The plastic channel system will contain the liquid plastic part. At this time, the mold cavity is in a closed state to do the task of forming the product.
Step 3: Cool the mold part so that the molten plastic part turns into a solid state. In order to get the plastic out, the melted plastic must be solidified. In this step, the machine’s cooling system will work to cool the mold and solidify the molten plastic.
Step 4: Take the product out. This is the final step of the injection molding process. The injection molding machine’s needle system will slowly pull out half of the mold, leaving a certain amount of time to take the product out. Then close the mold again to continue the new process.
Suitable plastics
The types of plastic commonly used in injection molding are thermoplastics, thermosetting plastics, and some elastomers. Available materials are usually metals or a mixture of materials, so designers can select the material with the most suitable properties.
Material selection criteria are based on stiffness, modulus of elasticity, flexural resistance, heat resistance and water absorption, design requirements as well as manufacturing cost, each with different specifications. should be considered and considered. The thermoplastics are nylon, polyethylene, and polystyrene. Thermosetting resins are epoxy and phenolic.
Structure of plastic injection molding machine
Clamping system
It has the effect of opening and closing the mold while supporting the movement of the molding element and creating a force large enough to hold the mold during the filling process and push the product out of the mold. The motion of this assembly is reciprocating, so any mechanism that produces this movement is allowed.
Common types of mold clamp assemblies include:
– Mechanical clamp assembly
– Hydraulic clamp assembly
– Mechanical clamp assembly with hydraulic combination
Mold
Consists of 2 basic components: a fixed half and a movable mold. The movable mold half usually carries the mold core, and the fixed mold half usually carries the mold cavity. In the mold plates, a cooling system and plastic channel are arranged. In addition, there are connecting rods and other parts such as a heating system … will talk about plastic injection mold in detail.
Spray system
The injection system consists of 3 parts: the feed hopper, the thermal cylinder, the screw, and the nozzle.
Feed Hopper
Thermoplastic is fed in the form of pellets. The feed hopper serves to contain these particles. These small particles of material from the door of the feed hopper enter the thermal cylinder.
Thermal Cylinder
The heating cylinder for the material makes the material molten, it is heated by the thermocouples.
The screw consists of 3 segments:
Inlet section: Near the inlet hopper used to move the material forward, at the end of this zone, the material softens and begins to flow.
Compression zone: In the middle of the screw, used to compress liquid materials.
Dosing area: Mix and homogenize the material before injection into the mold.
Nozzle: The part that attaches between the cylinder head and the nozzle of the mold. The nozzle must have a shape suitable for the flow of the material and be firmly attached to the nozzle during injection molding. The nozzle hole should be smaller than the nozzle hole in the mold.
The nozzle is interchangeable and has its own heating ring. Because the types of plastic have different characteristics, the nozzles also have different textures to help the best plastic injection process into the mold.
Advantages and limitations of using an injection molding machine
Advantage:
Complex shapes: Plastic injection molded parts can hold very tight tolerances on extremely small parts that are not possible with other manufacturing methods and cost-effectively. This allows injection molding products to be more complex or more suitable for certain applications.
Speed and scale: Injection molding works best when it quickly produces a large number of parts. The mold can contain multiple cavities all producing identical products in one press.
Usually, the cooling time of thermoplastics is also short. Even large parts can be produced in a minute or two. This means that every minute you can produce hundreds of products from one machine and one operator.
Durability: Plastic is an extremely durable material, especially when molded. That’s why it’s often used to make the outer shell or outer shell of equipment, plastic containers, etc. In addition, it is practically possible to mix anti-UV agents, increasing the anti-corrosion properties. bacteria, making it antistatic, and other uses make it a very durable material choice for components.
Product control: It is much easier to control the bonded surface of plastic molded components than other components. The colors are melted directly into the resin allowing for a uniform color without the need for a second operation such as powder coating. In addition, the mold can give the product many different characteristics, from smooth and smooth to matte..
In addition, labels and logos can be engraved on the part by the mold, making it easier for users to read and easily found on the product.
Defect:
Design Limitations: Since the mold has to be partially opened and ejected, there are some designs that cannot be molded or would be extremely difficult to cast.
High upfront costs: Injection molding involves an investment in an injection mold that can cost anywhere from 20 million to 500 million depending on the complexity of the part and the size of the mold.
Longer design time: Before production can be made entirely of drawings, molds must be designed and engineered to be able to rapidly increase project time and deliver products to production.
These are all information about how does injection moulding machine work that BNT shares with you. Hopefully, through our article, you will have more useful knowledge to apply to your work.
Contact information to buy an injection molding machine:
Address: No. 233, 23/10 Phuong Son Ward, Nha Trang City, Khanh Hoa
Hotline: 0905 361 004
Email: bntbaonam@gmail.com
Website: bnt-machinery.com
Fanpage: BNT Machinery